Case Study: Sensorized Bearings for Predictive Maintenance
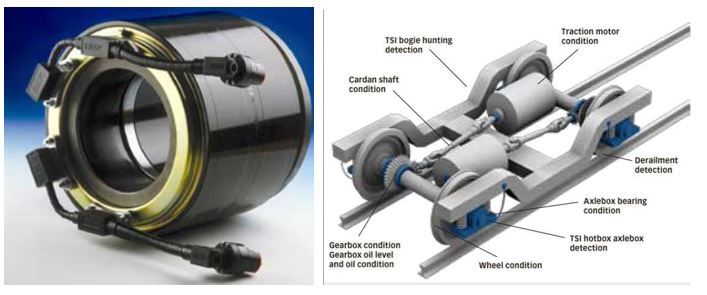
The Challenge
Critical rotating machinery in the automotive, rail, and industrial sectors relies on the health of bearing units. Traditional bearings offer no insight into their operational state, leading to maintenance schedules based on time rather than actual condition. This results in costly, unplanned downtime when bearings fail unexpectedly, or unnecessary replacements of perfectly good components.
Our Solution
5D Nexus specialized in the reverse engineering and enhancement of standard bearing units, transforming them into intelligent, sensor-integrated systems capable of providing real-time diagnostic data.
- Reverse Engineering and Design Optimization: We began by meticulously reverse-engineering existing bearing units to create precise 3D CAD models. This process included optimizing the design to accommodate sensors without compromising structural integrity.
- Sensor Integration: We integrated a suite of sensors to monitor key performance indicators, such as temperature for hotbox detection, vibration for derailment and bogie hunting detection, and sensors for gearbox oil levels and conditions.
- Automated CAD Processes: To accelerate the design-test-iterate cycle, we developed automated CAD scripts. These scripts allowed for rapid modifications and regeneration of complex 3D models and drawings, drastically reducing iteration time.
The Results
The development of these sensorized bearing units provided a significant leap forward in predictive maintenance capabilities for our clients:
- Enhanced Diagnostics: The integrated sensors provide continuous, real-time data, allowing operators to monitor the health of bearing assemblies and detect potential failures long before they become catastrophic.
- Reduced Unplanned Maintenance: By shifting from a time-based to a condition-based maintenance schedule, our clients significantly reduced unplanned downtime and associated costs.
- Improved Safety and Reliability: Early detection of issues like hotboxes and derailment risks enhances the overall safety and reliability of rail and automotive systems.
- Rapid Iteration: Our automated CAD processes enabled swift design improvements, allowing for quick adaptation to new sensor types or bearing models.