Case Study: Industrial Transformer Design & Value Engineering
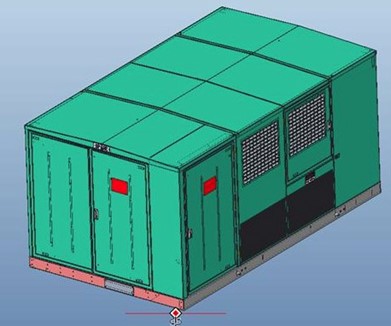
The Challenge
An Original Equipment Manufacturer (OEM) of industrial-grade transformers needed to re-engineer their flagship product line. The primary goals were to reduce manufacturing costs and improve thermal and structural performance without compromising the high reliability required for mission-critical industrial applications. This required a holistic approach, from detailed mechanical design of sheet metal enclosures to advanced performance validation.
Our Solution
5D Nexus undertook the complete mechanical design and development of the transformer systems, focusing on design validation and cost optimization through a multi-disciplinary approach.
- Detailed 3D CAD Modeling: Our engineers created comprehensive 3D models of the transformer structures, enclosures, and internal components using Creo and AutoCAD. This included detailed modeling of sheet metal fabrications using the Creo Sheet Metal module.
- Finite Element Analysis (FEA): We performed rigorous FEA simulations to analyze both thermal and structural performance. This allowed us to validate the design against operational loads, optimize heat dissipation, and ensure long-term structural integrity.
- Value Engineering (VA/VE): A systematic VA/VE process was implemented to analyze every component and manufacturing step. We identified opportunities to use more cost-effective materials, simplify designs, and streamline assembly processes, all while maintaining or enhancing performance.
- Design for Manufacturability (DFM): DFM principles were applied throughout the design phase. This included creating detailed 2D manufacturing drawings with comprehensive Bill of Materials (BOM) and ensuring that all components were designed for efficient, precision fabrication.
- Systems Integration: The mechanical design was carefully integrated with the transformer's complex electrical and control systems to ensure seamless assembly and functionality.
The Results
Our integrated engineering approach delivered substantial and measurable improvements for the client:
- Significant Cost Reduction: The value engineering and DFM initiatives led to a marked decrease in material and manufacturing costs per unit.
- Improved Manufacturability: The precision-fabricated components and optimized designs significantly improved production efficiency and reduced lead times for our OEM partner.
- Enhanced Reliability: FEA-driven design validation ensured the final product could withstand harsh industrial environments, enhancing its operational reliability and service life.
- Comprehensive Documentation: We delivered a complete package of fabrication drawings and detailed BOMs, enabling smooth and efficient production by manufacturing partners.
This project successfully demonstrates 5D Nexus's ability to combine detailed design with advanced analysis and strategic cost optimization to deliver high-performance, reliable, and commercially competitive industrial products.